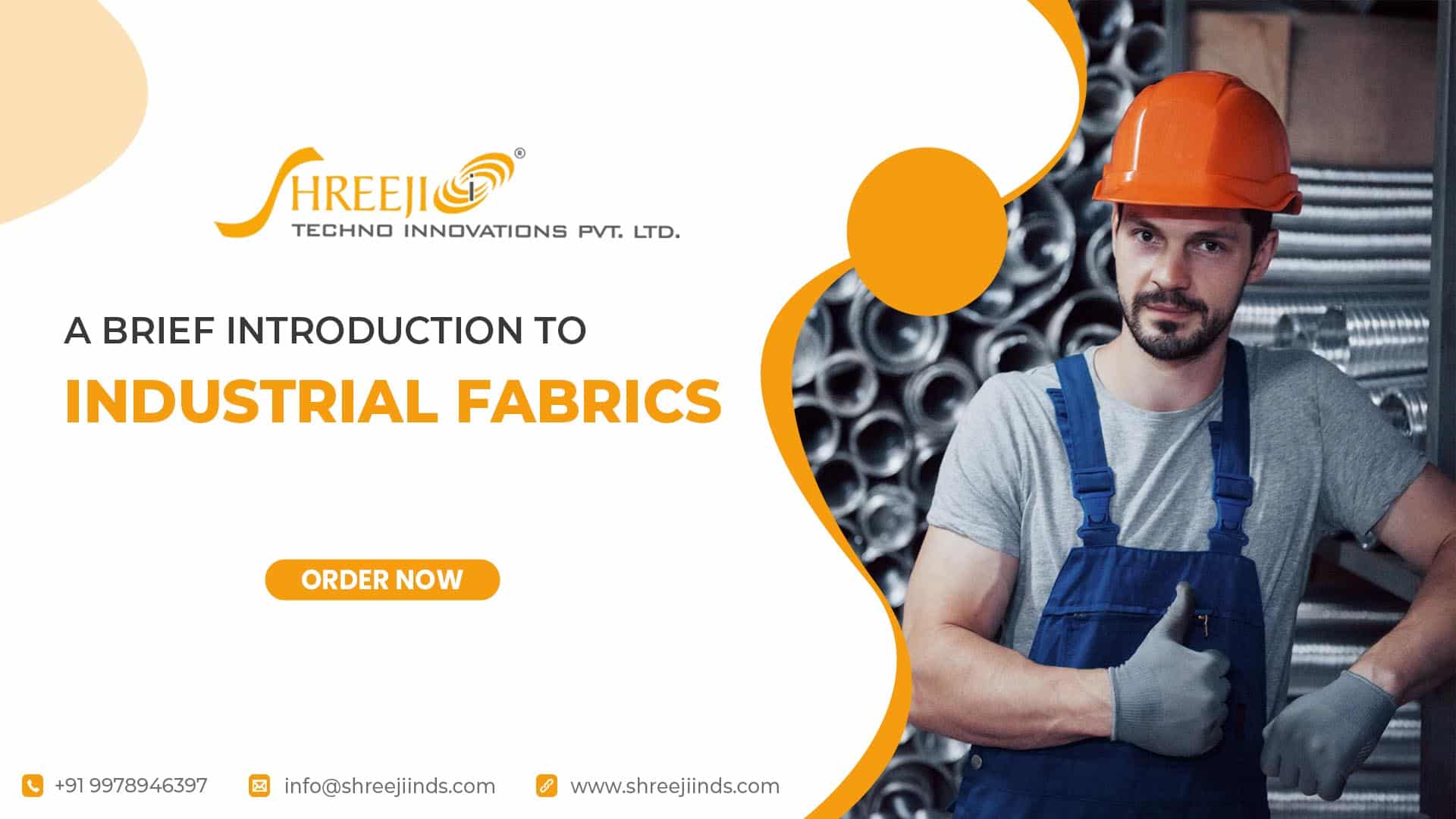
Industrial fabrics are created and constructed to be utilized in goods, operations, or services wherein functional needs take precedence over the aesthetic appeal often associated with textiles. Professionals from industries other than apparel employ them for demanding, high-performance applications. Industrial fabrics can be used as an essential part of another product to improve its strength, performance, and other attributes. They may also be employed in the production of goods or alone to carry out a single or a number of particular tasks. Textile (apparel) fabrics and industrial fabrics are distinct in a number of ways.
Higher performance fibers, yarns, and chemicals are used to make industrial fabrics in order to avoid failures that could have disastrous effects. The fabric must be able to manage the climatic conditions and structural constraints of the application, making functionality the most crucial feature. The inherent performance requirements of higher value fibers and materials might make them more challenging to work with, making the production of industrial fabrics more challenging. Glass fibers, for instance, are exceedingly abrasive. The average lifespan of the fabrics is increased by rigorous testing on a regular basis utilizing extremely precise and reliable tests.
Fiber vs Fabric
A fiber is a substance, either natural or manufactured, with an extremely high aspect ratio (length to breadth), which can be transformed by a variety of processes into a fabric. Fiber characteristics include length, size, and surface profile. Staple and filament are the two lengths of accessible fibers. The length of a staple fiber is limited or finite. The fiber’s length is expressed in centimeters or inches, and it might differ even within a fiber from the same source. Short fibers can be used to create staples for non-woven fabrics or twisted together to create yarn. A fiber with a limitless or seemingly endless length is called a filament. In yards or meters, the lengthy continuous filament fibers are measured. A tow is what is created when a filament is bundled and severed.
Natural vs Synthetic
Cellulose, the main structural element of plant and bacterial cell walls, is used to make natural fibers. Because they are made of protein, animal fibers are also regarded as natural fibers. Because the molecule has several polar hydroxyl groups which interact with nearby molecules, natural fibers have excellent structural integrity and are resistant to chemical attacks. It is possible to chemically alter natural fibers like cotton to create regenerated fibers like rayon and acetate.
Ceramics, metals, and glass are examples of inorganic materials. Fiberglass, which is constructed of spun glass and blended with epoxy resins to build reinforcing components for vehicles and boats, is a great example of this. Steel wool pads and ropes both contain steel fibers. By heating carbon at an elevated temp, graphite ribbons are produced, which are then compressed to form carbon fibers. Because of how strong and light the fibers are, they are more expensive. They are being taken into account for use in bicycles, autos, and golf clubs. Silver and gold can also be utilized as textile fibers.
Finally, polymers are used to make synthetic fibers. Strong and resistant to most substances, synthetic fibers can be engineered to have a wide range of performance qualities. A liquid chemical composition is pushed through spinnerets, solidified, and manufactured into a continuous strand of just about any length to create a synthetic fiber.